Is Your Heat Treatment System Treating the Atmosphere Badly?
The Project
There was awareness that releasing 1700°F (925°C) of combustion product up a stack provided for significant heat recovery and energy savings opportunities. This Continuous Heat Treat operation line consisted of a Hardening and Draw Furnace that ran at high temperatures yet it did not implement any heat recovery technology.
A natural gas consumption baseline was developed to benchmark current furnace operating efficiencies. Energy saving strategies and priorities were determined through a systematic analysis of the existing equipment.
Diagnosis and Findings:
- Poor control of Draw Furnace pressure
- Potential annual savings over 7 million cubic feet of natural gas on the High Heat/Draw Furnace
- Total energy savings identified by the audit was projected at $110,000 on an annualized basis
“From waste heat to 7 million cubic feet of natural gas savings shows that hiring the experts will save you thousands in energy costs within a few years payback!”
– Russ Chapman, President, Firebridge Inc., 2019
The Firebridge Solution
Using the Six Delta™ Method to gain an optimised perspective, Firebridge identified several performance improvement opportunities. The Six Delta™ Method is a comprehensive approach through a systematic analysis which considers improvements over six interdependent focus areas. This method is data driven by metrics from each focus area which combine to drive a strong business case.
The Six Delta™ focus areas for this project are:
Primary: Energy Consumption – Product Quality – Process Production – GHGe Emissions
Secondary: Safety & Compliance – Equipment Reliability
Solutions Implemented:
A case was made to capture the waste heat generated by the Hardening Furnace and use it to heat the Draw Furnace.
- Provided the engineering, procurement, construction, and system commissioning to redirect 1700°F flue gases from the Hardening Furnace to the Draw Furnace
- Eliminate the need to dilute the exhaust with inside air, reducing the local exhaust by 1,700 SCFM
- Ducts and fan sized to minimize the negative pressure in the High Heat Furnace
- Provided internally insulated duct work to eliminate thermal expansion issues

Improved results were found across all Six Delta™ focus areas.
Safety & Compliance
- New system meets current safety and compliance standards
Quality
- Improve the cold air leaking into the High Heat Furnace by sealing
Productivity
- Installation and commissioning during summer shut-down
- Total payback period 1.8 years
Energy Consumption
- Fuel consumption was reduced by 31% on the Draw Furnace
Reliability
- Minimized negative pressure in the High Heat Furnace
- Internally insulated ducting eliminated thermal expansion issues
Greenhouse Gas Emissions
- GHGe emissions reduced by 31%
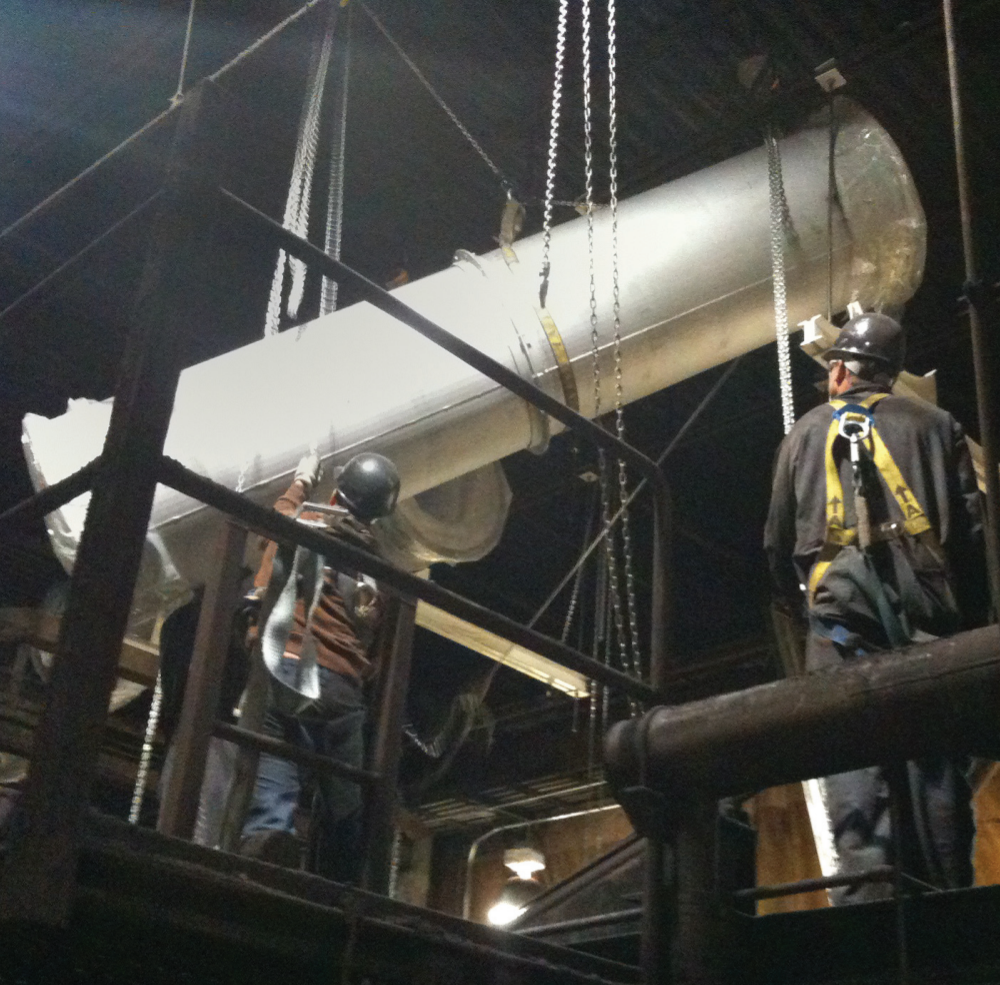
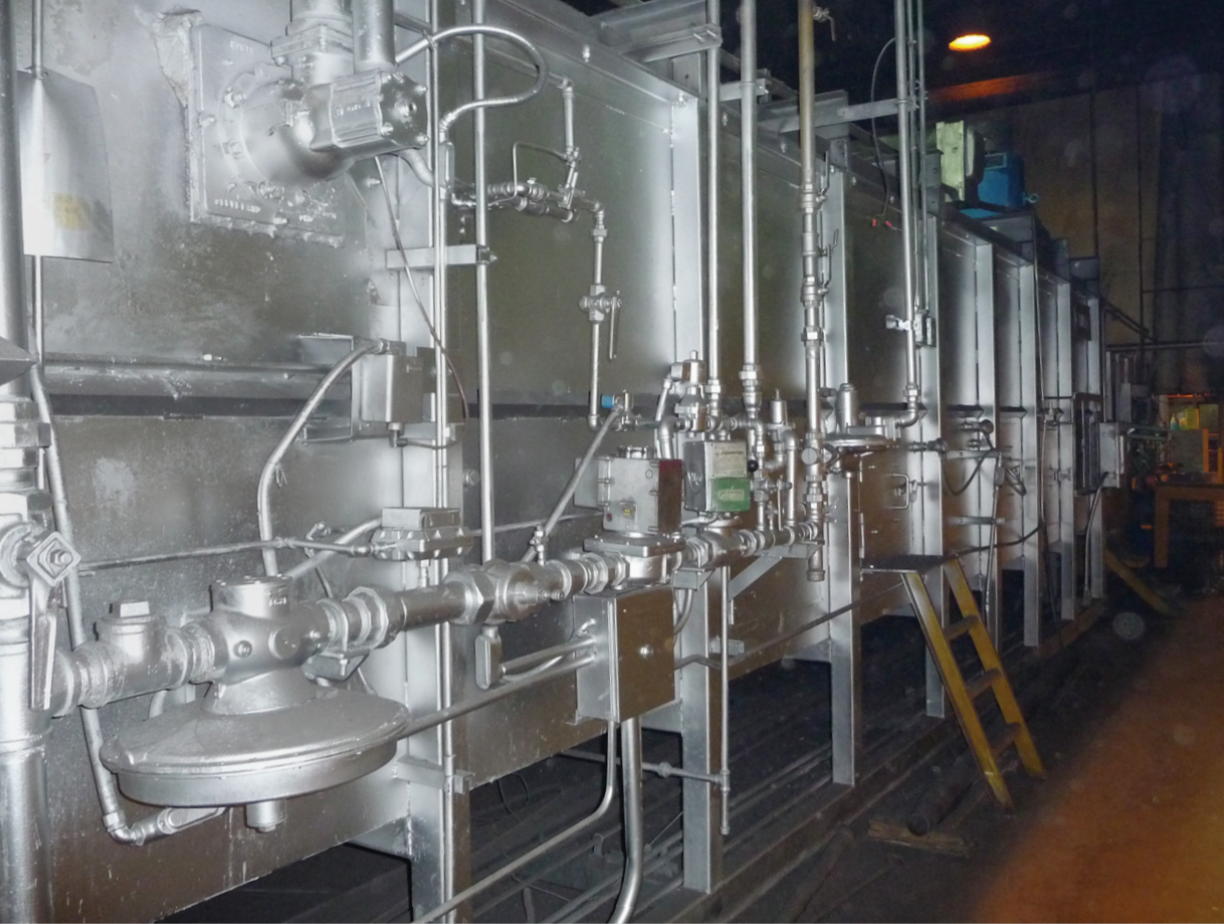
Liked what you read? Stay up to date with new content by Subscribing below!